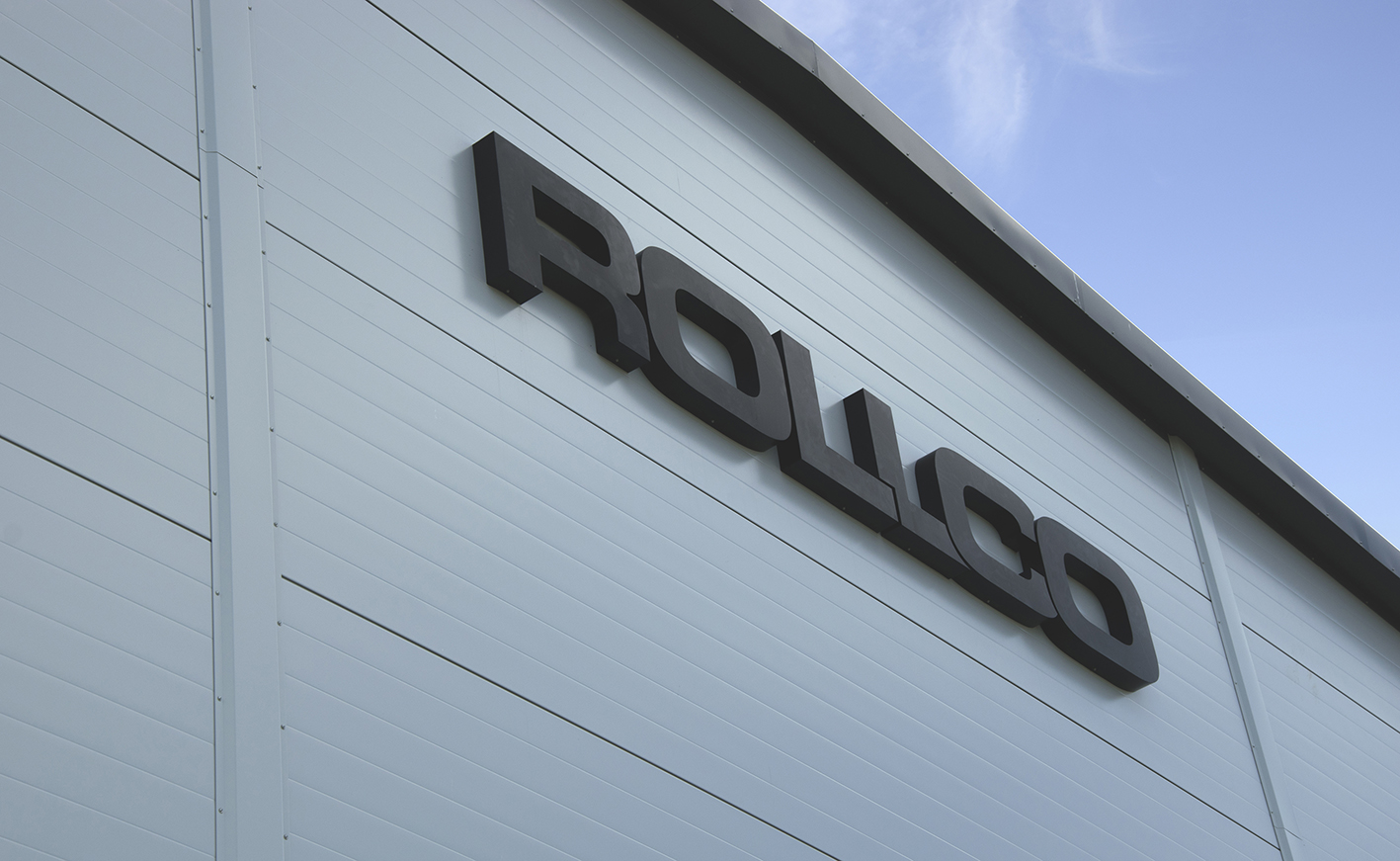
The corona crisis frees up time for Rollco in Helsingborg. It is used to update digital documents and streamline automation, where a digital configurator plays a key role. It cuts lead time, says designer Oskar Friberg.
Helsingborg-based Rollco, a manufacturer of linear systems and automation solutions for industry, is responding to the crisis with efficiency improvements. Corona frees up time for us, says designer Oskar Friberg.
We have grown rapidly and now that inquiries are decreasing, we are intensifying our digitalization efforts. We are now working on optimizing the basis for our information flows to be more efficient throughout the chain, from sales and quotes to manufacturing and delivery.
Every day, products and goods are moved in industry using Rollco belt conveyors and linear systems. They are customized and tailored to meet the customer’s specific needs and Rollco has a rich component library that provides a wide range of options.
Twenty times faster with the configurator
However, developing proposals takes time, which increases the more advanced the solution the customer wants. Therefore, the process has been automated with a digital configurator in collaboration with KonfigDesign. The configurator brings together data from the CAD database and the ERP system in an efficient way.
We did a time study that showed that it takes one hour for one person to produce an ordinary and customized conveyor, says Oskar. The configurator does the same in under five minutes.
Thanks to automation, the process is more than 20 times faster. The seller benefits from this. Instead of collecting all the data at the customer’s premises, going to the office to calculate a transportation solution and preparing a quote that is then sent to the customer to wait for a response, the salesperson can present a solution directly to the customer, who can make a decision quickly. This saves further valuable time.
Configurator makes CAD data easy to manage
An important link for everything to work is a special module that makes the CAD data manageable for Monitor ERP, Rollco’s business system. So no matter how complex the data is or how much data it contains, the module ensures that the amount of information is adapted to the business system so that the salesperson can easily produce the quote during the customer visit.
Working in this standardized way also supports Rollco’s production by providing a uniform basis. It also supports product development.
The configurator helps us to ensure that all our processes are right from the start and that we can eliminate the human factor. This means less time at each stage,” says Oskar.
During the current coronavirus crisis, the configurator documentation is being updated to further streamline tender management and other processes. Working with automation and the configurator helps to cut lead time, which has positive effects throughout the company. As requests start to come back after the pandemic, Rollco is breathing a sigh of relief and can better respond to customer requests.
When the corona is over, we will be better equipped,” says Oskar.
Are you also interested in a configurator for your business?
Feel free to contact us, or read more about how we can help you here